Muesli machine
Supertek developed the first fully automatic production line for individual muesli for the customised food market. This is a muesli machine for 80 different ingredients that was installed for Mymuesli GmbH in Passau as a global innovation in 2011 and since then has produced 566 billion customised muesli varieties successfully and efficiently.
Customers can make up their favourite customised muesli from many different ingredients via the website with an online shop. Typical ingredients that can be selected for the personal muesli mix are muesli bases, such as oat flakes, wheat flakes and flakes but also fruits, such as strawberries, apples, dates, raisins or special items such as nuts, almonds, seeds, chocolate and much more.
Each muesli package or muesli box can be filled fully automatically in the muesli machine with another recipe.
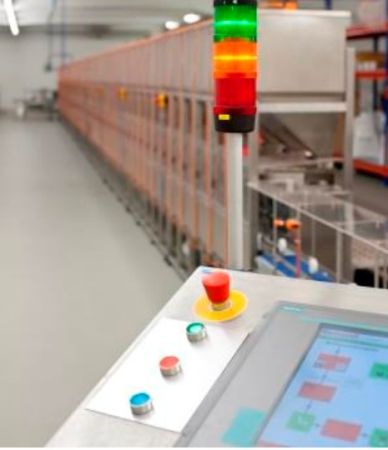
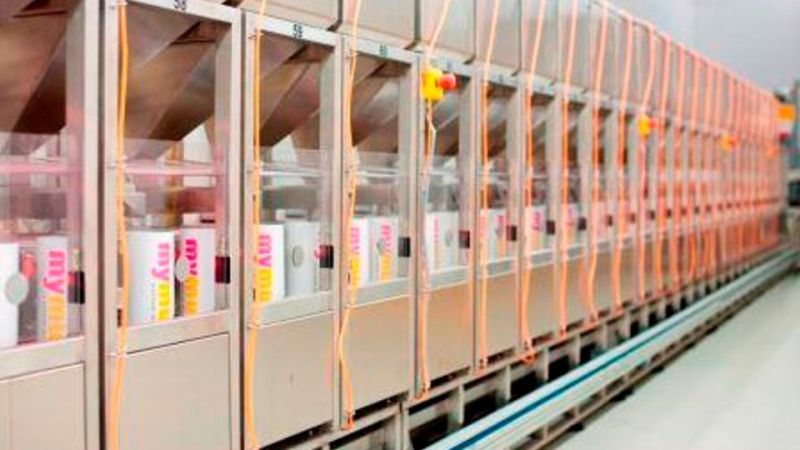
The individual ingredients are dispensed via self-contained filling stations that are installed next to each other in a production line. Each muesli station has a storage container or hopper to save the ingredient, a vibration and conveying channel to fill the ingredient, a transport system to convey the containers, a scanner to identify the muesli container and scales to weigh the ingredient accurately and to dispense it into the container.
After the order for the personal muesli mix has been received at the Internet shop the orders are processed automatically in the muesli machine.
At the start of the production line each container receives an individual label with the ingredients, information on the ingredients, the best before date and a 2D bar code for automatic production and traceability in compliance with the Foodstuffs Information Ordinance (LMIV).
After the containers have been labelled in a labelling machine, they go through the filling station and are accurately filled with the selected muesli ingredients. The ingredients are mixed, the containers closed and sealed, weighed on the calibrated scales and packed with Supertek's production line too. A very hygienic design is guaranteed due to the entirely stainless steel finish and food-safe components. The energy costs and sound emission are very low due to the fully electronic energy design and not using pneumatics.